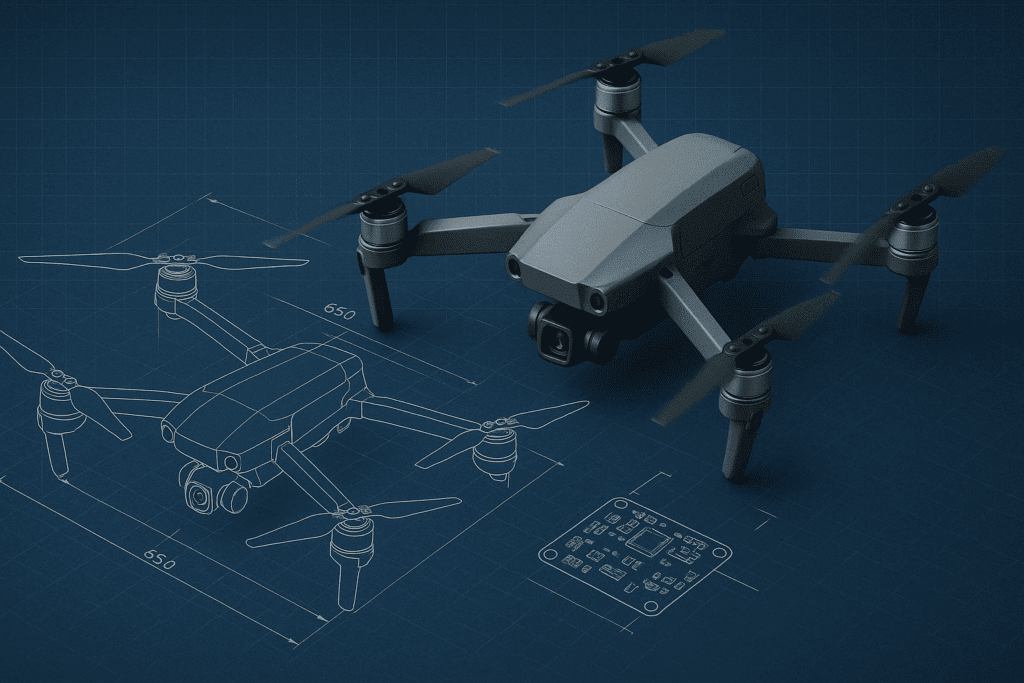
The drone industry is moving faster than ever. According to the Civil Aviation Ministry, as the global drone industry grows, the Indian drone industry is expected to reach INR120-150 billion (USD1.5-1.9 billion**) by 2026. From logistics and surveillance to precision critical commercial operations and recreational use, drones are no longer just niche tech models- they are solutions to various challenges. But behind the slick software and automated expertise lies a set of engineering fundamentals that don’t often make headlines: aerostructures, mechanical design, and system integration.
These hardware disciplines are not just important but absolutely essential for performance, reliability, and scalability in unmanned aerial systems.
Aerostructures: Built to Perform
Aerostructures refer to the primary and secondary structural components of a UAV and are crucial in determining the drone’s performance, efficiency and safety. In real-world applications, drones need to be lightweight yet robust. That’s where materials like composites and advanced alloys come in. They allow for longer flight durations and higher payload capacities without compromising structural integrity.
Optimizing the shape and structure of components enhances flight stability and maneuverability which is an essential factor not just for high-precision use cases like aerial mapping or inspection, but even for general operations in unpredictable environments. Stability directly affects the quality of data or imagery collected, especially in critical sectors like surveying, construction, or environmental monitoring.
Moreover, today’s drones are expected to be able to carry payloads like cameras, sensors, and communications equipment. Aerostructural design has to account for that, ensuring these systems can be integrated seamlessly and safely. The trend is clearly moving towards modularity, enabling easy upgrades, flexible configurations, and simplified maintenance. That kind of versatility is fast becoming an industry standard.
Mechanical Design: Power, Precision, and Practicality
Mechanical designs are all about selecting and configuring the right components—motors, linkages, gears—to translate electrical power into efficient movement. These parts must not only deliver propulsion but also endure constant mechanical stress, temperature fluctuations, and terrain-specific challenges.
Well-thought-out mechanical design improves weight distribution and overall aerodynamics, which in turn affects how stable and responsive a drone is in flight. Whether you’re flying in a densely built urban space or a wind-swept plateau, the drone’s ability to stay balanced and respond to control inputs in real-time is critical.
Good mechanical design is also about ease of production and maintenance. Using tools like Computer-Aided Design (CAD) and Finite Element Analysis (FEA), engineers can simulate conditions and fine-tune every component for performance and manufacturability. This reduces cost, speeds up development, and ensures structural robustness.
And in the field, repairability matters. If a component fails or a drone needs an upgrade, streamlined mechanical systems allow for fast servicing and part replacement, minimizing downtime.
System Integration: Making Complex Tech Work Together
A drone isn’t a single technology, it’s an ecosystem. From flight control and propulsion to GPS, sensors, communications, and payloads, each part has to be in sync with the others seamlessly. That’s where system integration comes in. It brings all these elements together into one unified, mission-ready platform.
Modern drones use advanced software and onboard systems that need to be in perfect sync. Whether it’s enabling autonomous flight, ensuring obstacle avoidance, or streaming real-time video, every subsystem must perform flawlessly in coordination with others. In fields like surveillance, logistics, or emergency response, even a split-second delay or system mismatch can compromise the mission.
Integration is also what makes drones adaptable. As applications diversify from precision farming to industrial inspections users need drones that can scale with their needs. For example, in aerial surveillance and mapping, integrated systems allow drones to gather and process data more efficiently, providing valuable insights in real time. A modular, integrated platform allows operators to swap in new payloads or upgrade processing capabilities without redesigning the whole system.
With AI and machine learning becoming integral to drone operations, drones can now analyze data in real time, improving decision-making processes and operational efficiency.The ability to add new layers of intelligence on top of the hardware is what’s pushing drones into their next evolutionary phase.
What This Means for the Industry
As the UAV space matures, headlines will continue to focus on AI, connectivity, and autonomy. But none of that will function without the right hardware foundations.
For drones to be more than just flying gadgets—for them to be dependable, versatile tools across sectors—we need to build deeper capabilities in aerostructures, mechanical design, and system integration. These aren’t just back-end functions—they are strategic enablers of innovation.
If we get the hardware right, everything else follows. Because the future of flight isn’t just autonomous. It’s engineered.
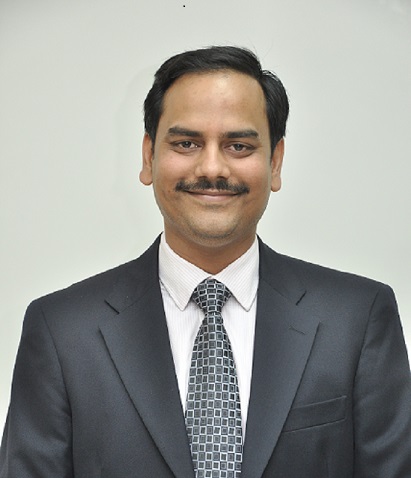
Sachin Mathur is the Head of Human Resources at ideaForge, a leading Indian drone technology company. With over 20 years of HR experience across the Drone, Automobile, Aviation, and ITES sectors, he has led initiatives in HR strategy, organizational development, talent management, and M&A integration. Sachin holds an MBA from MGM Institute of Management, a Master’s degree from Indira Gandhi National Open University, and certifications from IIM Bangalore and the University of Minnesota.
Leave a Reply